(1) The mounting plate is a relief plate with a soft texture. The printing plate is in direct contact with the plastic film, and the printing pressure is relatively light. So the flatness requirement for flexible plates is higher than that for metal convex plates.
The installation program is as follows
(1) Before cleaning the printing plate roller and pasting the printing plate, it is necessary to clean the surface of the roller that holds the printing plate with a fine cloth. If there are oil stains or dust, gasoline can be used for scrubbing.
(2) The plate base for cleaning the printing plate should not have oil stains or residue of photosensitive polymer, as this will affect the adhesion of the double-sided tape. Be careful not to let the solvent come into contact with the surface of the photosensitive layer.
(3) Adhesive tape: Take double-sided tape and remove the protective film on the surface; Place the printing plate on one side of the adhesive tape, then cut off the tape and stick the other adhesive surface onto the appropriate position of the printing plate roller. Pay attention to the correct position and avoid tilting. The entire board should be firmly attached
(4) After the edge of the sealed printing plate is attached, the surrounding area should be tightly sealed with adhesive to prevent oil from entering the plate and prevent the adhesive tape from losing its bonding force and peeling off during the printing process.
(2) Printing
(1) Flexographic printing pressure should be light, with clear graphics and text as the standard. Due to excessive pressure, the flexible version is squeezed, causing lines and dots to spread outwards, resulting in thicker lines, enlarged dots, and blurry images. If the printing pressure is too light, the graphics and text will be unclear and not thick, resulting in dryness and thinness. When adjusting the pressure of the flexible plate, the following points should be noted: ① the flatness of the printing plate; ② The pressure between the mesh roller and the printing plate roller; ③ The pressure between the embossing roller and the printing plate should be tangential on the surfaces of the two rollers, and the pressure at both ends of the rollers should be consistent with that in the middle. In short, the mesh roller, plate roller, and embossing roller all need to meet the requirements of having straight shafts and concentric circles.
(2) The ink used in flexographic printing ink is mainly alcohol soluble ink, and the main ink solvents are ethanol, isoamyl alcohol, butanol, and isobutanol
(3) The printing tension is too high, which is beneficial for color matching, but the film will shrink after printing, which can easily cause deformation of the dots; On the contrary, if the printing tension is too low, the image color matching is not easy to be accurate.
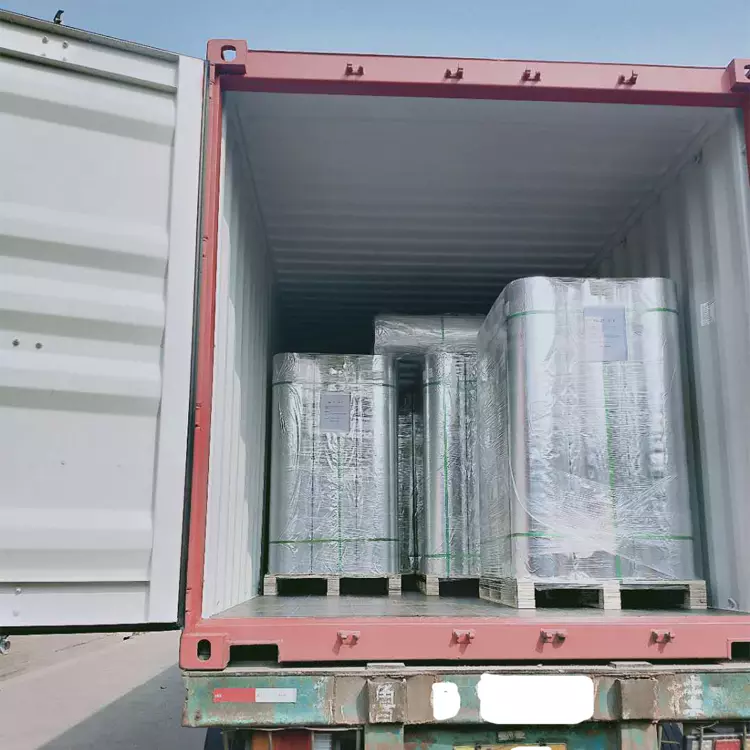