Polymer blend refers to a mixture of two or more homopolymers or copolymers, especially plastic blends. Although plastics have many excellent properties, they still have many disadvantages compared to metal materials. In some fields that require high comprehensive performance, a single plastic is difficult to meet the requirements. Therefore, plastic blending has been implemented and developed. The purpose of blending modified plastics is as follows: to improve the comprehensive performance of plastics; Improve the mechanical properties of plastics, such as strength, low-temperature toughness, etc; Improve the heat resistance of plastics. The thermal deformation temperature of most plastics is not high, and for some components that work at a certain temperature, general-purpose plastics are difficult to handle; Improving processing performance, such as the poor formability of polyphenylene oxide (PPO) and the significant improvement in processing flowability after modification with polystyrene (PS); Reduce water absorption and improve the dimensional stability of the product, such as the high water absorption of polyamide, which causes dimensional changes in the product; Improve the combustion resistance of plastics. Most plastics are flammable materials with low safety when used in electrical and electronic equipment. By flame retardant modification, the safety of materials can be improved; Reduce the cost of materials, especially engineering plastics, which are expensive. By blending low-priced general-purpose plastics with engineering plastics for modification, the cost of materials is reduced and the processability of engineering plastics is improved; To achieve the functionalization of plastics and improve their performance, such as the low conductivity of plastics, for some applications that require anti-static and conductive properties, they can be blended with conductive polymers to obtain plastic materials with anti-static, conductive, and electromagnetic shielding functions, meeting the requirements of electronics, home appliances, communications, military, etc.
Acrylonitrile styrene butadiene copolymer (ABS) resin is known as a blend modified material for polystyrene. This new type of material is strong and tough, overcoming the prominent brittleness of polystyrene. In addition, ABS resin has good corrosion resistance, is easy to process and shape, and can be used to prepare mechanical parts, making it one of the most important engineering plastics. Therefore, ABS resin has aroused great interest and attention, thus opening up a new field of polymer science in polymer blending modification. In 1975, DuPont developed the ultra-high toughness polyamide Zytel-ST, which is a blend made by adding a small amount of polyolefin or rubber to polyamide, resulting in significantly improved impact strength compared to polyamide. This discovery is very important. It is now known that other engineering plastics such as polycarbonate (PC), polyester, polyoxymethylene (POM), etc. can significantly improve their impact strength by adding a small amount of polyolefin or rubber.
In short, through blending modification, the comprehensive performance of plastics can be improved, and the variety of plastics can be increased with relatively low investment, expanding the use of plastics, reducing the cost of plastics, achieving high performance, refinement, functionalization, specialization, and serialization of plastics, promoting the development of the plastic industry and polymer materials industry, and also promoting the development of high-tech industries such as automobiles, electronics, electrical appliances, communications, military, aerospace, etc.
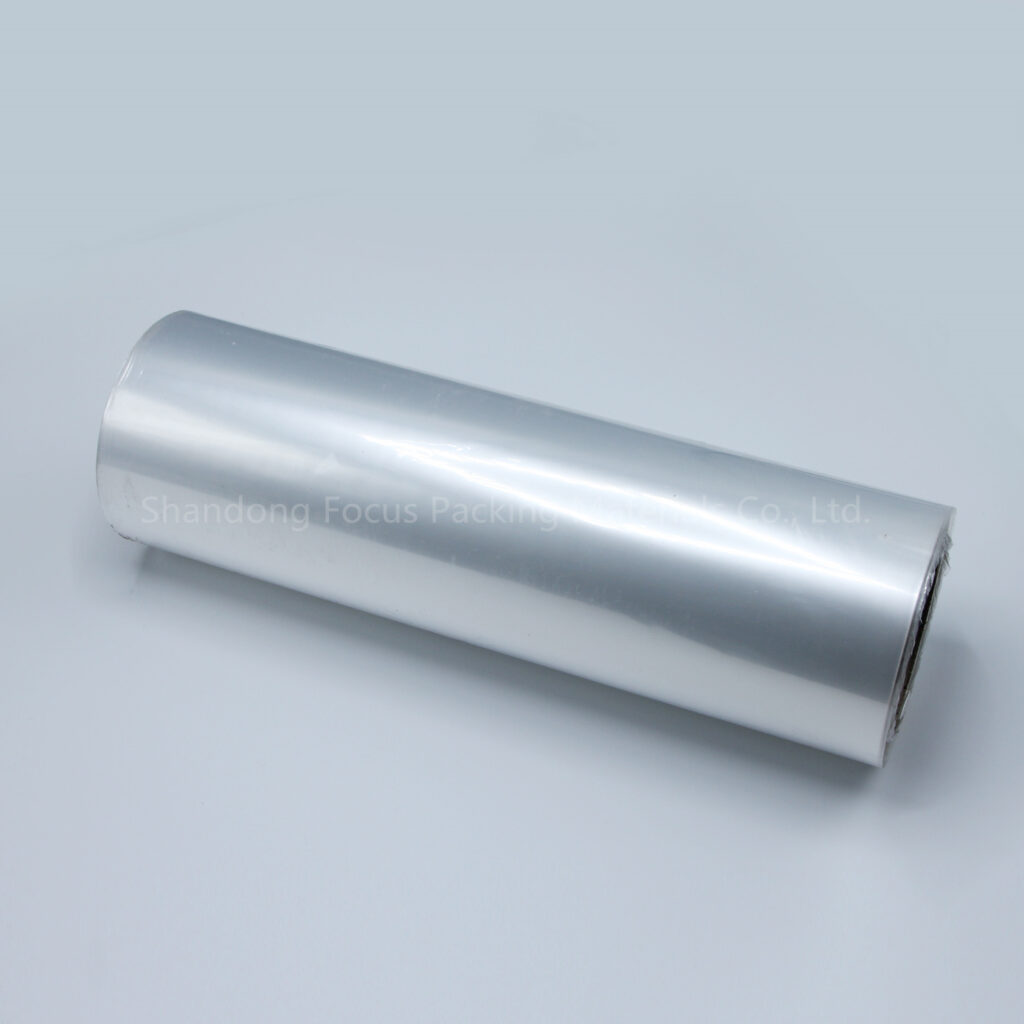