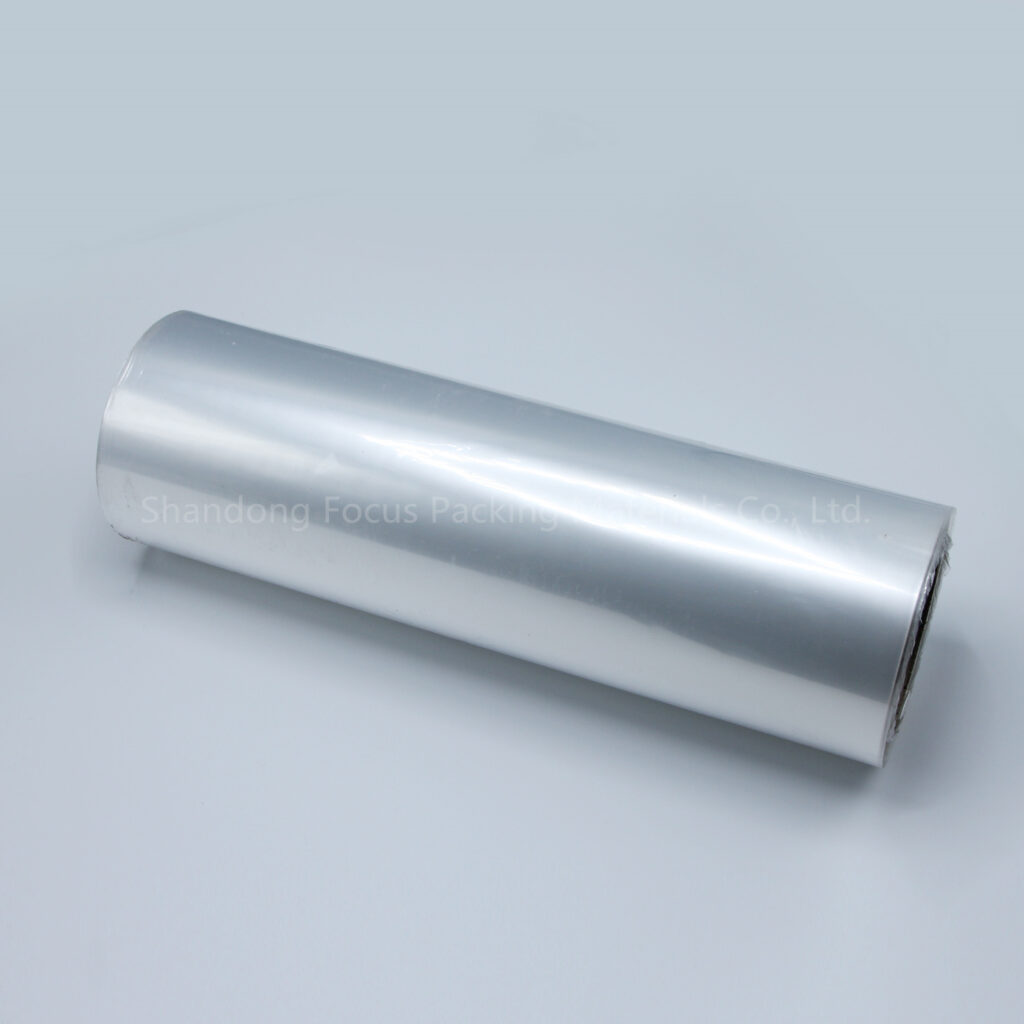
Extrusion casting composite film is a process of using a T-shaped die of an extruder to cast a thermoplastic onto other substrate films. After being cooled and pressed by a cooling roller, it becomes a multi-layered composite film. In order to improve the adhesion between the extruded plastic and the substrate film, an anchor coating agent (AC) should be applied to the substrate film
The production process of extrusion casting lamination is as follows: unwinding the substrate film → applying AC agent back to the eye, drying one layer, and extruding PE, EVA, PP and other plastics with a T-shaped die of an extruder. At the same time, the second substrate film is hot melted and pressed on the pressure roller under the condition that the extruded plastic is the intermediate layer and bonding layer. After cooling, it is rolled up into a three-layer structure packaging material. There are single-stage, two-stage, and multi-stage forms of extrusion casting layer method. That is, two or three extruders are connected in series on a production line, and a multi-layer composite packaging film bag with more than three layers can be extruded and cast at once. The bag box made of 5-100pm thick aluminum foil and paper composite can be used for packaging cream, artificial cream, chewing gum, fertilizer, etc. It can be used for packaging pastries, pharmaceuticals, PE, and other products, and can also be used as a container for packaging. Its physical and mechanical properties.